Aluminum welding methods: Almost all welding methods can be used to weld aluminum and aluminum alloys, but aluminum and aluminum alloys have different adaptability to various welding methods, and each welding method has its own application. The gas welding and electrode arc welding methods are simple and easy to operate. Gas welding can be used for the repair welding of aluminum sheets and castings that do not require high welding quality. Electrode arc welding can be used for repair welding of aluminum alloy castings. Inert gas shielded welding (TIG or MIG) method is the most widely used aluminum and aluminum alloy welding method. Aluminum and aluminum alloy sheets can be tungsten electrode AC argon arc welding or tungsten electrode pulse argon arc welding. Aluminum and aluminum alloy thick plates can be used for tungsten helium arc welding, argon-helium mixed tungsten gas shielded welding, melting electrode gas shielded welding, and pulse melting electrode gas shielded welding. Melting electrode gas shielded welding and pulsed melting electrode gas shielded welding are more and more widely used (argon or argon/helium mixed gas). Guangdong Aluminum Plate Wholesale
Preparation before welding
1. Cleaning before welding: when welding aluminum and aluminum alloys, the oxide film and oil stain on the welding port of the workpiece and the surface of the welding wire should be strictly removed before welding;
1) Chemical cleaning Chemical cleaning has high efficiency and stable quality. It is suitable for cleaning welding wire and workpieces of small size and mass production. Two types of dip method and scrub method are available. Use acetone, gasoline, kerosene and other organic solvents to degrease the surface, wash with 5%~10% NaOH solution at 40℃~70℃ for 3min~7min (pure aluminum time is slightly longer but not more than 20min), rinse with flowing water, and then use The 30% HNO3 solution at room temperature to 60°C is pickled for 1 min to 3 min, rinsed with flowing water, and air-dried or dried at low temperature.
2) Mechanical cleaning: When the workpiece is large in size, the production cycle is long, and it is contaminated after multi-layer welding or chemical cleaning, mechanical cleaning is often used. First wipe the surface with acetone, gasoline and other organic solvents to remove oil, then directly use a copper wire brush or stainless steel wire brush with a diameter of 0.15mm to 0.2mm until the metal luster is exposed. Generally, it is not advisable to use grinding wheels or ordinary sandpaper to prevent sand particles from remaining on the metal surface and entering the molten pool during welding to produce slag inclusions and other defects. In addition, scrapers, files, etc. can also be used to clean the surface to be welded.
If the storage time is too long after cleaning (such as more than 24h), it should be reprocessed.
2. Backing plate: aluminum alloy has low strength at high temperature, good flowability of liquid aluminum, and weld metal is prone to collapse during welding. In order to ensure the penetration of the weld without collapsing, the welding plate is often used to support the molten pool and nearby metals. The backing plate can be graphite plate, stainless steel plate, carbon steel plate, copper plate or copper rod. A circular arc groove is formed on the surface of the backing plate to ensure that the welding seam is formed on the reverse side. It can also be formed by single-sided welding and double-sided molding without pads, but requires advanced welding operations or advanced technological measures such as strict automatic feedback control of arc welding energy. 3. Preheating before welding: thin and small aluminum parts generally do not need to be preheated. Preheating before welding can be carried out when the thickness is 10mm to 15mm. According to different types of aluminum alloys, the preheating temperature can be 100°C to 200°C, and oxygen-acetylene can be used. Flame, electric furnace or blowtorch heating. Preheating can reduce the deformation of weldment and reduce defects such as blowholes. Aluminum alloy wholesale manufacturers after welding
1) Cleaning after welding The residual flux and welding slag left in the welding seam and nearby after welding will destroy the passivation film on the aluminum surface, and sometimes corrode the aluminum parts, and should be cleaned. Workpieces with simple shapes and general requirements can be cleaned by simple methods such as hot water flushing or steam blowing. For aluminum parts with high requirements and complicated shapes, wash them with a bristle brush in hot water, and then immerse them in a chromic anhydride aqueous solution or potassium dichromate solution at a concentration of 2% to 3% at 60°C to 80°C for 5 minutes ~10min, scrub with a bristle brush, then wash in hot water, dry in an oven, or blow dry with hot air, or dry naturally.
2) Post-weld heat treatment Aluminum containers generally do not require heat treatment after welding.
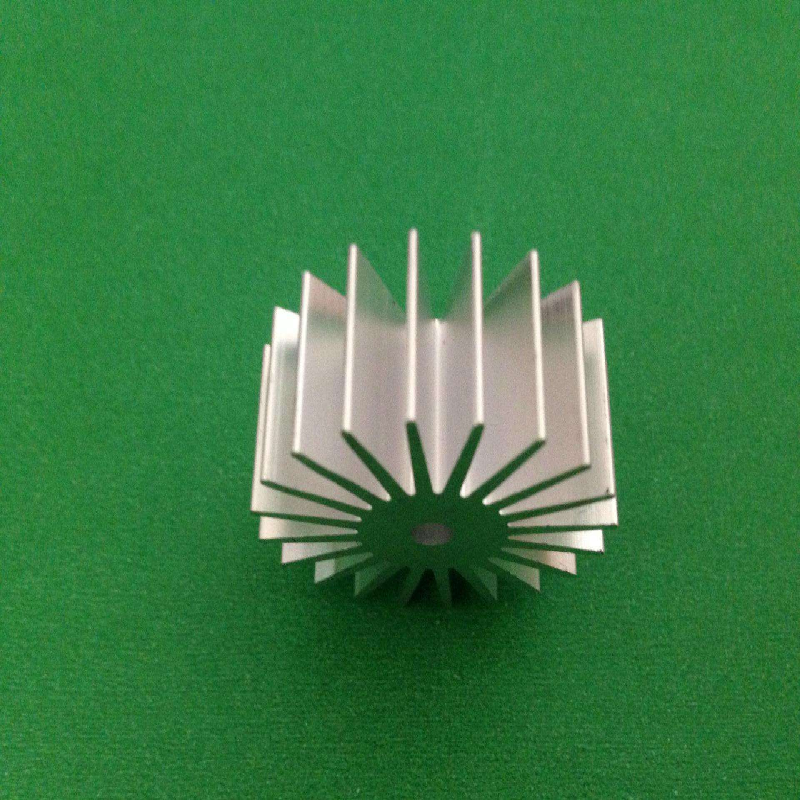
What’s your reaction?
Love0
Sad0
Happy0
Sleepy0
Angry0
Dead0
Wink0